What is Porosity in Welding: Comprehending Its Causes and Enhancing Your Skills
What is Porosity in Welding: Comprehending Its Causes and Enhancing Your Skills
Blog Article
Porosity in Welding: Identifying Common Issues and Implementing Finest Practices for Avoidance
Porosity in welding is a prevalent concern that usually goes unnoticed till it creates substantial troubles with the stability of welds. In this discussion, we will certainly explore the essential variables adding to porosity formation, analyze its detrimental results on weld efficiency, and discuss the best techniques that can be taken on to reduce porosity incident in welding processes.
Common Reasons For Porosity
Another frequent offender behind porosity is the presence of pollutants externally of the base steel, such as oil, oil, or corrosion. When these impurities are not effectively removed before welding, they can evaporate and come to be caught in the weld, creating problems. Making use of dirty or wet filler materials can present pollutants into the weld, contributing to porosity concerns. To alleviate these common root causes of porosity, detailed cleaning of base metals, proper securing gas option, and adherence to ideal welding specifications are important techniques in attaining top notch, porosity-free welds.
Influence of Porosity on Weld Top Quality

The existence of porosity in welding can dramatically endanger the architectural honesty and mechanical residential properties of bonded joints. Porosity creates voids within the weld metal, weakening its total strength and load-bearing capability.
Welds with high porosity levels often tend to display lower impact toughness and minimized capacity to warp plastically prior to fracturing. Porosity can impede the weld's ability to properly transfer pressures, leading to premature weld failure and possible safety and security dangers in essential frameworks.
Ideal Practices for Porosity Prevention
To improve the architectural stability and high quality of bonded joints, what specific procedures can be carried out to reduce the event of porosity throughout the welding process? Making use of the appropriate welding technique for the certain product being bonded, such as changing the welding angle and gun setting, can better stop porosity. Routine assessment of welds and prompt remediation of any type of issues determined during the welding process are essential practices to prevent porosity and generate high-quality welds.
Significance of Proper Welding Methods
Carrying out appropriate welding techniques is extremely important in guaranteeing the architectural integrity and high Related Site quality of bonded joints, building upon the structure of efficient porosity prevention steps. Excessive warm can lead to boosted porosity due to the entrapment of gases in the weld pool. Furthermore, utilizing the appropriate welding parameters, such as voltage, present, and take a trip rate, is critical browse around here for accomplishing sound welds with marginal porosity.
Moreover, the selection of welding procedure, whether it be MIG, TIG, or stick welding, ought to align with the details demands of the job to guarantee optimal outcomes. Proper cleaning and preparation of the base steel, along with choosing the best filler product, are additionally essential parts of efficient welding methods. By sticking to these finest methods, welders can decrease the risk of porosity development and generate high-quality, structurally audio welds.
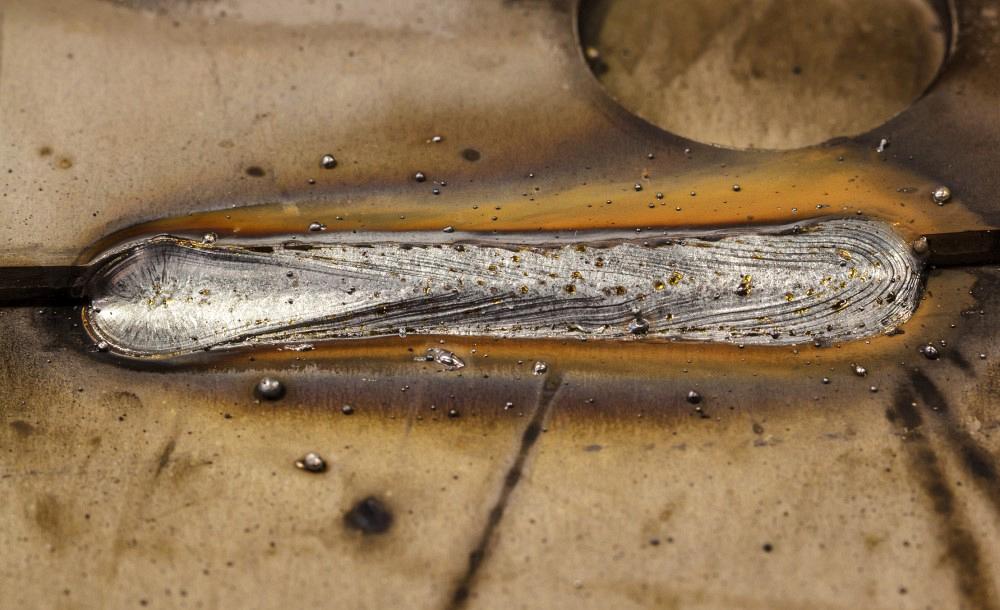
Testing and Quality Assurance Steps
Checking procedures are important to discover and prevent porosity in welding, making certain the strength and resilience of the final product. Non-destructive screening approaches such as ultrasonic testing, radiographic screening, and aesthetic evaluation are frequently utilized to determine potential flaws like porosity.
Post-weld inspections, on the other hand, examine the final weld for any type of issues, including porosity, and validate that it satisfies defined requirements. Applying a comprehensive high quality control plan that includes extensive testing treatments and inspections is critical to minimizing porosity problems and making sure the general top quality of bonded joints.
Verdict
Finally, porosity in welding can be a typical issue that impacts the high quality of welds. By determining the typical reasons of porosity and carrying out best techniques for prevention, such as Get the facts proper welding methods and testing procedures, welders can make sure premium quality and dependable welds. It is necessary to focus on prevention methods to minimize the occurrence of porosity and preserve the integrity of welded frameworks.
Report this page